Peanuts can be eaten after simple processing, and deep processing can also be made into nutritious food and health products. The first step in processing is peanut shelling. Peanut shells can be used for bio-power generation as fuel instead of coal, and can also be comprehensively utilized for deep processing to add value. In recent years, with the adjustment of agricultural structure, the peanut planting area has been continuously expanded, and the output of peanut has increased year by year. When peanuts are pressed for oil, deep processing, and used as export commodities, the peanut needs to be shelled, and the application of peanut shelling machines is increasing year by year. We have also received many orders from abroad. In October, this year we received orders from customers in Zimbabwe, the Philippines, and Zambia.
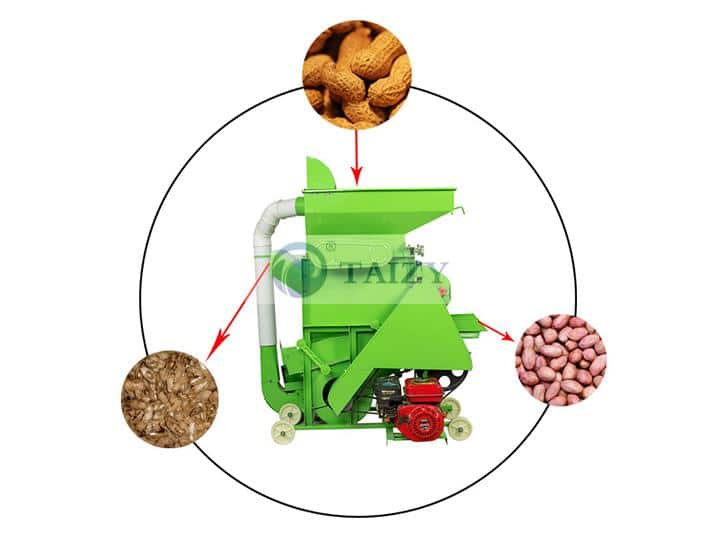
Peanut sheller sold to Zimbabwe
groundnut shelling machine in Zimbabwe
This customer is in Zimbabwe. He asked our company about the peanut sheller through a friend in Xinjiang and wanted a 600 kg/h peanut. According to his needs, we recommended model TBH-800 to him. It only took one month from the time the customer asked us the details of the machine to the time the customer received the machine. At the same time, we also introduced to this customer the problems that should be paid attention to when using the groundnut shell removing machine and the maintenance.
Precautions When Operating Groundnut Shell Removing Machine
- When peanuts are fed, they must be fed evenly, in an appropriate amount, and continuously. They must not contain iron filings, stones, and other debris to prevent crushing of peanut kernels and mechanical failure. When the peanut kernels cover the sieve surface, the outlet switch can be turned on.
- A peanut shelling machine equipped with a cleaning device, and must have a high degree of cleanliness. The loss rate should be low and the breakage rate should be low. It has a certain versatility and can be used for peeling a variety of crops to improve the utilization rate of the machine. Choose a suitable screen according to the size of peanuts
- Requirements for peanuts. Peanuts should be dry and wet properly. Too dry will result in a high breakage rate, and too wet will affect work efficiency. In order to make it proper humidity, the following methods can be used: First, shelling in winter. The warm water evenly sprayed on the peanuts before peeling, then covered with plastic film, and then dried in the sun to shell. The second is to soak the dry peanuts in a large pool, and remove them immediately after soaking, and cover them with plastic film, and then dry them in the sun, finally peeling them when they are proper humidity.
- When the crushing rate exceeds 5.0%, increase the shelling roller gap; if the shelling is not clean, decrease the shelling roller gap. The gap adjustment is controlled within 25~40mm.
- During operation, do not stand on the side of the belt drive to avoid injury. The outlet of the shell should follow the wind direction, and it is strictly forbidden to stand behind the exhaust outlet.
- When the machine is running, hands or other parts of the body must not touch any moving parts, such as shafts and fans. It is strictly forbidden to reach into the feeding port and other dangerous moving parts
Maintenance of Peanut Sheller
- The peanut sheller is driven by a V-belt. After the new belt is used for some time, it will gradually become loose under the action of tension, so it needs to be adjusted according to the actual situation, and adjust the tensioning and tensioning wheel.
- When the machine is in use, pay attention to the operation of each part. Check whether the fastening bolts are loose, and if they are loose, tighten them in time. Attention should be paid to whether the fan blades are worn or broken, whether the external reinforcement plate of the blade is worn or deformed, if any problems are found, it should be repaired and replaced in time.
- The bearing parts should be checked for oil shortage or wear in time. If there is an oil shortage and wear, the oil should be replaced in time.
- After use, a large-scale inspection of the machine is required. After the inspection is completed, repair the damaged parts, clean the residues in the machine, oil the bearings, remove the belts, and put the accessories in the warehouse for next use.