Sesame Seed Peeling Machine丨Automatic Black Sesame Dehuller
Sesame Seed Peeling Machine丨Automatic Black Sesame Dehuller
Sesame Peeler Machine | Sesame Dehulling Machine
Features at a Glance
The sesame seed peeling machine is a kind of high-efficiency equipment integrating soaking, stirring, peeling, and separating, which is widely used in the field of food processing, such as black sesame, white sesame, and so on.
With compact design and convenient operation, this equipment can ensure that the color of sesame seed particles is white and the integrity rate is over 95%. It can realize 80%-85% peeling rate, which is the ideal sesame processing equipment for food processing factories, fried food factories and so on.
Highlights of sesame seed peeling machine
- Vertical cylinder design, internal composite layered structure (peeling bin + cleaning bin), occupies an area of only 1/3 of the traditional equipment.
- Composite stirrer through the axial propulsion + radial dispersion + ring turning, to ensure that the sesame in the process of peeling uniform force, no residual dead ends, peeling rate is stable up to 80% or more.
- Integrated PLC control panel, adjustable soaking time (10-30min), water flow intensity and other parameters.
- The finished sesame kernel is white and bright, suitable for sesame paste, sesame oil, baking ingredients and other high value-added product lines.
- Equipped with circulating water filtration system and negative pressure dust removal device, water consumption is reduced by 60%, dust emission ≤ 10mg/m³.
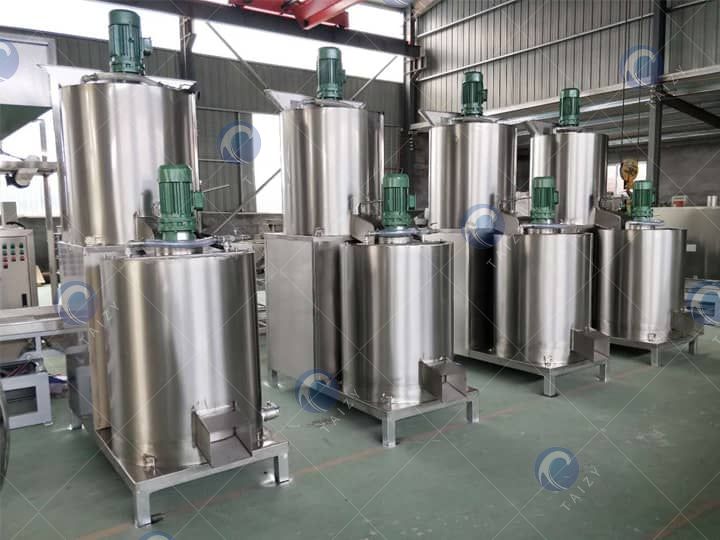
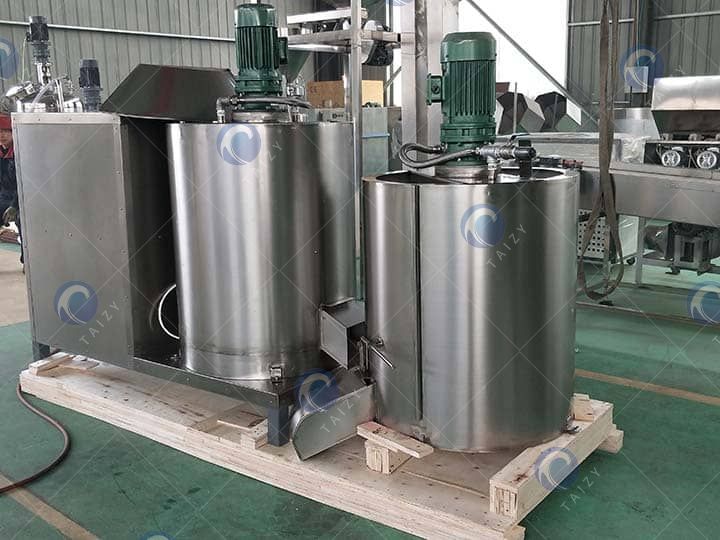
Black sesame dehuller structure and principle
- Reducer: drive the compound agitator to rotate.
- Double stirring barrel: complete the process of soaking, stirring and peeling sesame seeds.
- Compound agitator: produce axial, radial and circular turning, improve the peeling efficiency.
- Separation sieve plate: to realize the separation of sesame skin and seed kernel.
- Inlet and outlet: to facilitate the circulation and discharge of sesame, skin and water.
- Water filling pipeline system: used to control the water quantity in the soaking and cleaning process.
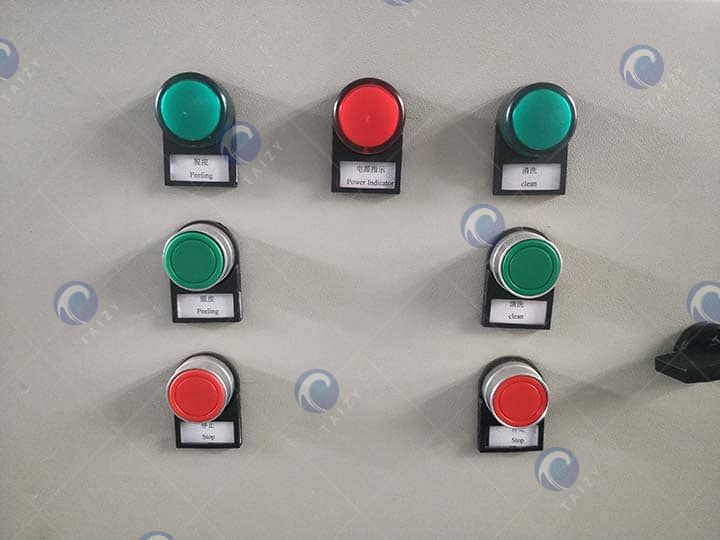
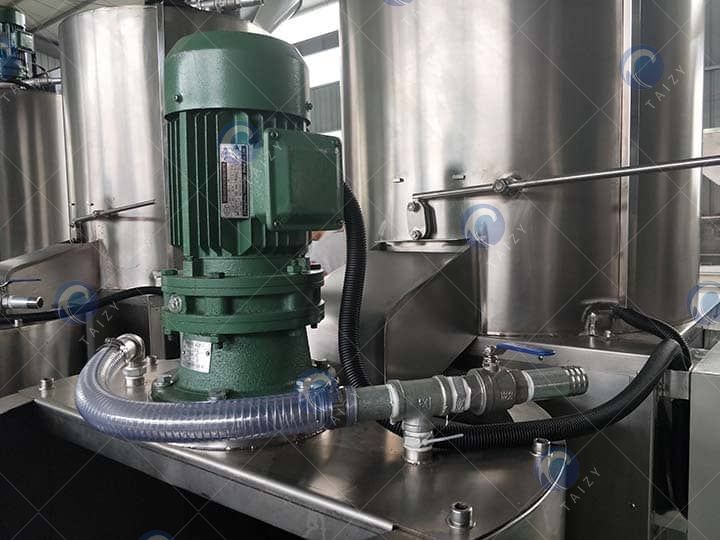
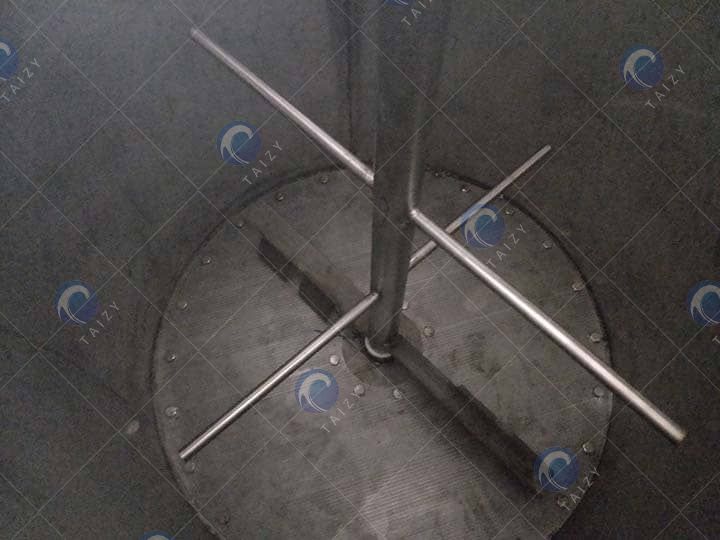
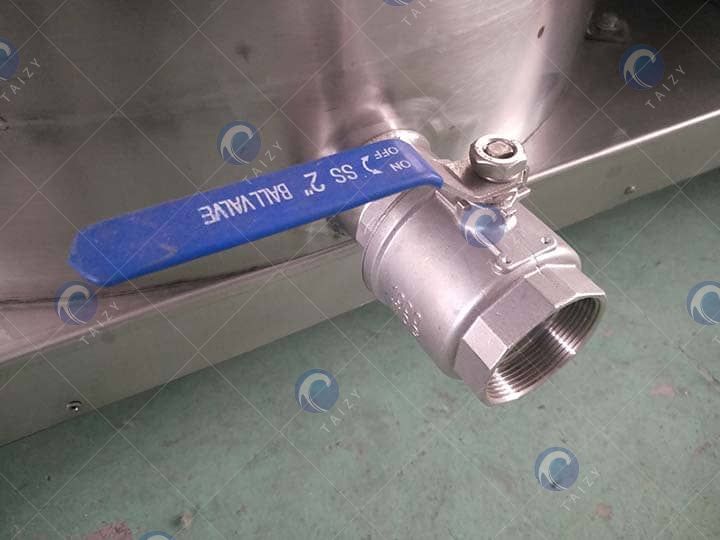
Working steps of sesame seed peeling machine
- Soaking pretreatment: soak sesame seeds mixed with appropriate amount of alkaline water (or hot water) for 10-13 minutes.
- Stirring peeling: pour the soaked sesame seeds into the peeling bucket, start the stirrer for 3-5 minutes of high-speed peeling.
- Separate the skin from the kernel: use the separating sieve plate to retain the seed kernel and remove the peeled sesame seeds.
- Into the washing drum: sesame seeds enter the washing drum through the valve, add about 1/3 water (sesame seeds: water = 3:1), stirring for 5-10 minutes.
- Cleaning and draining the skin: open the bottom drain valve, drain the skin while feeding the water to make sure the sesame kernel is clean.
- Discharge collection: open the discharge port after draining, collect the processed sesame kernel.
Sesame seeds do not need to be peeled when grinding sauce and squeezing oil, and when used in the food industry should be peeled.
Sesame husking machine technical parameters
Machine name | Sesame dehulling machine |
Power | Dehulling motor 2.2kw , Separating motor 1.5 kw |
Capacity | 400-500kg/h 30-50kg/barrel |
Dehulling rate | 80%-85% |
Weight | 500kg |
Size | 1400*700*2000mm |
Machine material | Made of Stainless steel |
Purpose of peeling sesame
Sesame may not be peeled in general oil production, but if directly consumed or used for further processing, peeling is particularly important. The reasons are as follows:
- The outer skin of sesame seeds contains high fiber and oxalate (about 2%-3% calcium oxalate complex), which are not easily absorbed by the body.
- Peeled sesame seeds are more easily digested and absorbed by the body, with higher utilization of protein and minerals.
- Peeled sesame seeds are white in color, fine in texture, better in taste, and more suitable for sesame sauce, sesame paste, pastries and other food production.
Wide application of peeled sesame
Peeled sesame has a wide range of applications, mainly in food and catering-related industries. Such as bread, burgers, biscuits, Shaqima, tahini, sesame oil, flour cakes, etc.
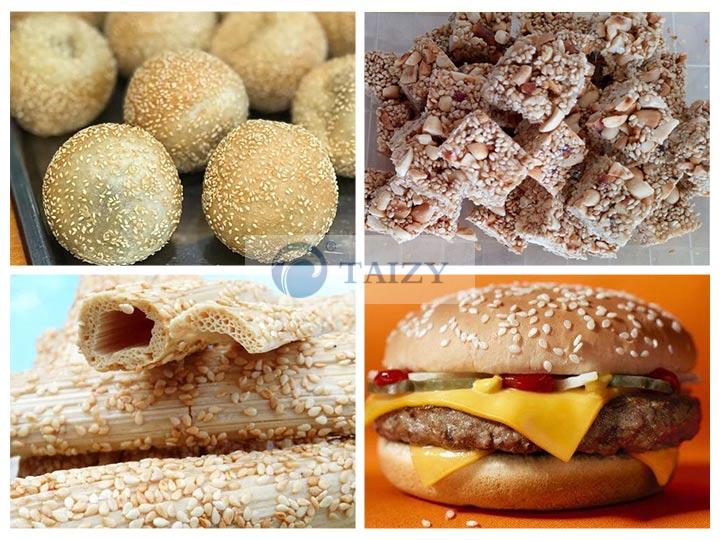
Sesame dehulling machine installation and maintenance
Installation requirements:
- For initial installation, the sesame seed peeling machine should be close to a water source, a power source, and good drainage facilities.
- Connect the inlet pipe to the water source. If the water pressure is not enough needs to be equipped with a booster pump.
- After connecting the power supply, check whether the equipment operates normally.
Daily maintenance:
- Clean up the sesame seed peeling machine residue after each use, and keep the machine body tidy.
- Flush the surface of separation screen with water, if there is any blockage, use high pressure water gun to flush.
- The speed reducer needs to change the lubricating oil regularly to ensure smooth operation.
- Regularly check whether the parts are worn out, and replace the consumables (such as blades, screen mesh, etc.) in time.
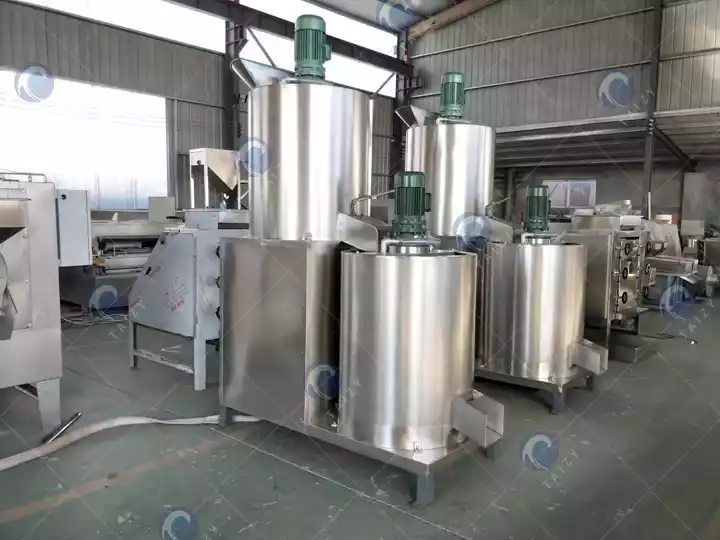
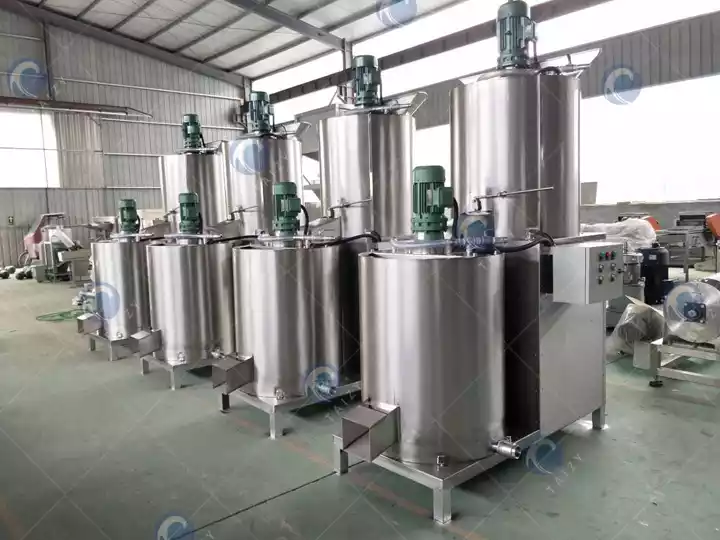
Other applications of sesame cleaning and peeling machine
A sesame seed peeling machine can also be used to peel pumpkin seeds. The principle of pumpkin peeling is the same as that of sesame peeling, and the same machine is used.
It’s just that different people will call different names. Some people will specifically call him a pumpkin seeds dehulling machine. So let’s take a look at how the pumpkin is peeled, and the effect of peeling.
Sesame skin peeling machine sold to Tanzania
One of our customers comes from Tanzania. He operates a sesame processing plant, which sells dehulled sesame seeds to various food processors.
According to his capacity needs, we suggest 5 sets of the sesame seed peeling machine to work at the same time. Below are the packing and shipping pictures.
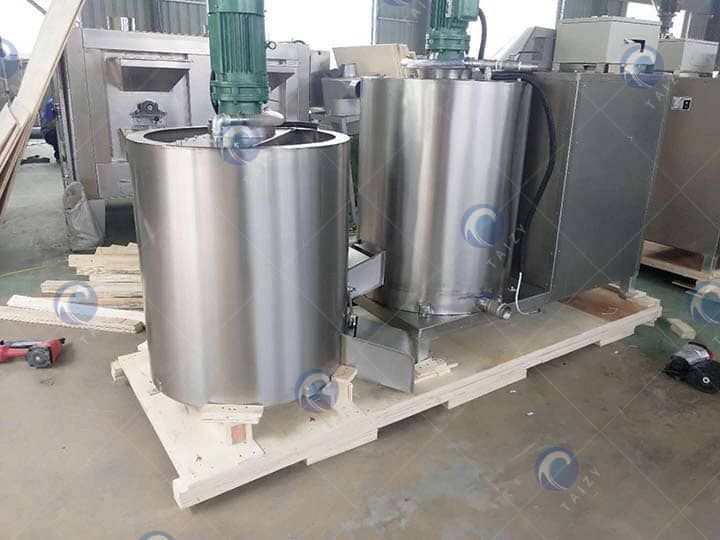
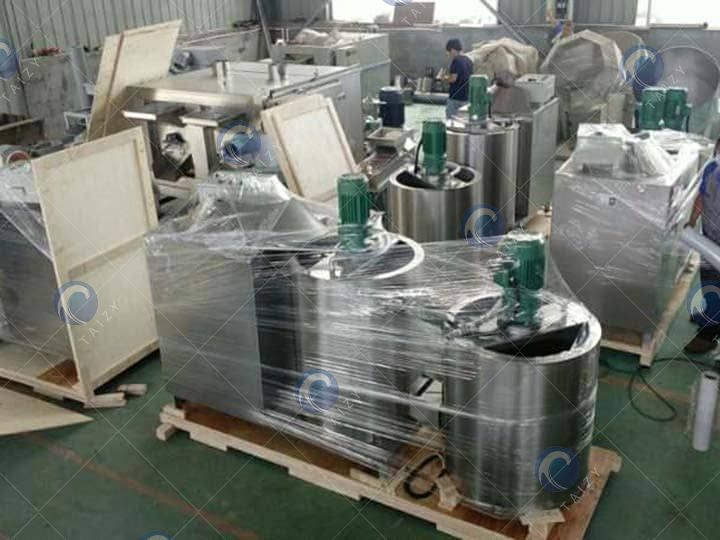
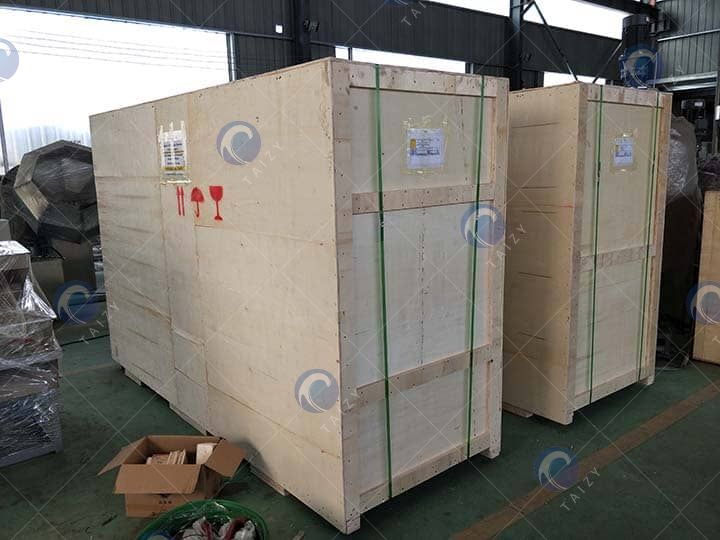
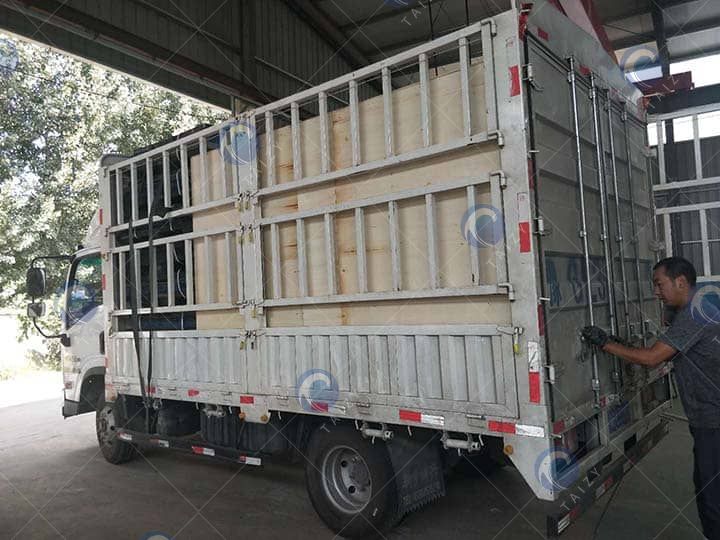
If you have any questions or needs about this sesame seed peeling machine, please feel free to contact us. We promise to reply quickly and answer all your questions patiently and are dedicated to providing you with professional support and service. We look forward to cooperating with you!